Rotary’s new R5000HD Commercial Truck Alignment System was designed to make aligning heavy-duty trucks, buses and other vehicles easy. One way it does this is by eliminating the need for rolling compensation that is required by other systems.
Growing numbers of fleets, truck dealers and independent repair facilities are interested in adding heavy-duty wheel alignment to their shops. There’s a low cost of entry for a service that can provide a solid ROI. But choosing the best equipment for the job is crucial to accuracy, efficiency, ergonomics and profitability.
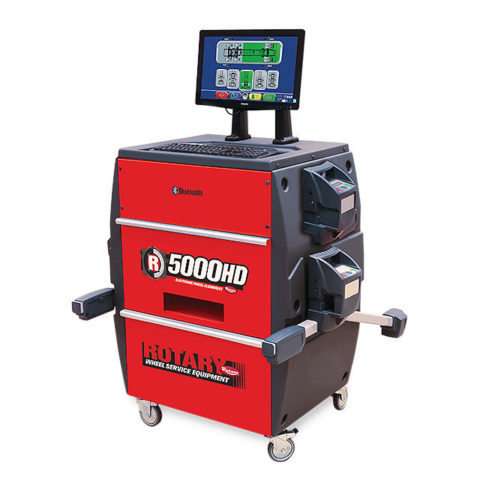
The new Rotary R5000HD Commercial Truck Alignment System was designed to make aligning heavy-duty trucks, buses and other vehicles easy. It takes the guesswork out of alignments and significantly reduces labour time when aligning vehicles with a GVWR of 19,500 pounds and above.
“Many heavy-duty shops are looking to increase revenue by adding wheel alignment services or improving their alignment efficiency,” says Jeff Vervoort, Rotary wheel service sales and technical trainer. “Heavy-duty alignment is a lucrative business. The average cost for a typical wheel alignment on a car is about $100-$120, but for a tractor trailer, it’s $250 and up, so the equipment can pay for itself pretty quickly.”
Rotary’s new R5000HD Commercial Truck Alignment System was designed to make aligning heavy-duty trucks, buses and other vehicles easy. One way it does this is by eliminating the need for rolling compensation that is required by other systems.
Typical alignments are performed by attaching a four-point clamp to the outer edge of the wheel. Unfortunately, if the wheel is damaged, the clamp is being mounted to an untrue surface. The result can be an inaccurate alignment unless technicians perform the time-consuming and sometimes back-breaking process of compensation. Rolling compensation is done by physically rolling the vehicle backward to allow the alignment head spindle to turn approximately 45 degrees and then rolling it forward. This reading is then used to calculate the vehicle spindle position to confirm the accuracy of the alignment.
Rotary’s R5000HD alignment system contacts the wheel at the bolt circle, which is the strongest, truest portion of the wheel, instead of the outer edge. That takes the guesswork out of alignments, and eliminates the added labour time, expense and physical effort associated with compensation. The results are a better bottom line and a safer work environment.
The system also significantly reduces labor time by electronically measuring axle offset on every alignment. Most other systems require the technician to manually measure axle offset, often wasting 10 to 20 minutes just to find out the truck has no issue. The Rotary R5000HD automatically measures axle offset and notifies the technician when there is a problem.
The system is ideal for aligning trucks with a GVWR of 19,500 pounds and above. It doesn’t require a tower at the front of the bay, has no minimum bay size requirements and the portable aligner console can be conveniently positioned anywhere in available bay space – floor, pit or lift.
The R5000HD features infra-red transmission among measuring heads. Each measuring head has controls to allow technicians to control the alignment process without having to return to the console, which can be located up to 59 feet away.
The control unit houses the computer, printer, monitor and accessories, and allows for recharging of the measuring head batteries.
For more information about the full line of Rotary wheel alignment systems visit www.rotarylift.com/Wheel-Service/Wheel-Alignment/ or call (800) 640-5438.
0 Comments