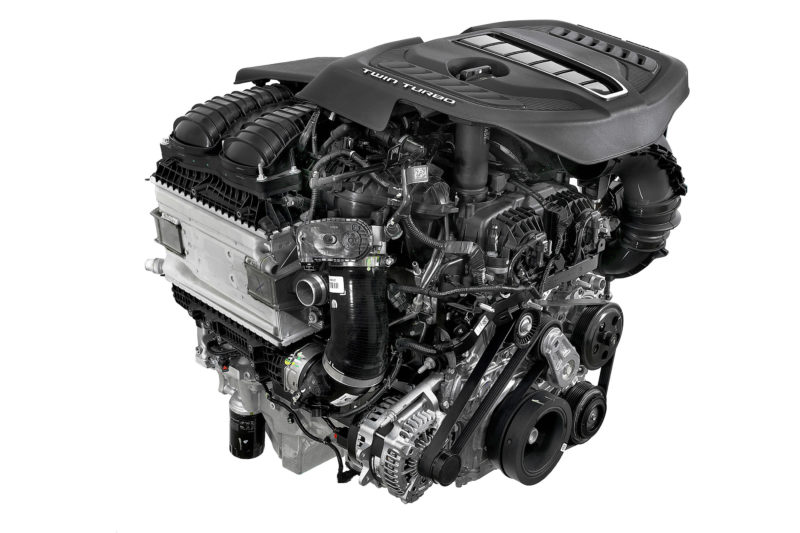
Even as it commits billions of dollars and a big part of its reputation on being a significant player in the BEV field, Stellantis is touting the ongoing investment in internal combustion engines (ICE) with its new Hurricane twin-turbo inline 6 that can produce more than 500 hp in high-output configuration.
Stellantis revealed its new, 3.0-liter, twin-turbo, inline, six-cylinder engine, named Hurricane, saying it delivers better fuel economy and fewer emissions than larger engines while at the same time generates more horsepower and torque than many competitors’ naturally aspirated V-8 and boosted six-cylinder power plants.
Designed with an inherently smooth-running I-6 configuration and state-of-the-art technology, the Hurricane twin-turbo’s robust base architecture enables Stellantis propulsion systems engineers to create two distinct variants:
- Standard Output (SO): Optimized for fuel economy, including the use of cooled exhaust gas circulation (EGR), while delivering enhanced power and torque (more than 400 hp/450 lb.-ft. of torque)
- High Output (HO): Optimized for great performance (more than 500 hp/475 lb.-ft.) while maintaining significant fuel economy during heavy use, such as towing.
The Hurricane twin-turbo achieves this V-8-rivaling performance while being up to 15% more efficient than larger engines, says the automaker.
“As Stellantis aims to become the U.S. leader in electrification, with a 50% battery-electric vehicle (BEV) sales mix by 2030, internal combustion engines will play a key role in our portfolio for years to come and we owe it to our customers and the environment to provide the cleanest, most efficient propulsion possible,” said Micky Bly, Stellantis head of propulsion systems.
“The Hurricane twin-turbo is a no-compromise engine that delivers better fuel economy and an important reduction in greenhouse gases without asking our customers to give up performance.”
Reducing greenhouse gas emissions is one part of Stellantis’ commitment to cut its carbon footprint by 50% by 2030 and to lead the transportation industry by achieving Net Carbon Zero by 2038. Those goals are key elements of the Stellantis Dare Forward 2030 strategic plan.
Specific horsepower and torque ratings will vary based on vehicle. The first vehicles powered by the Hurricane twin-turbo I-6 reach dealership showrooms this year.
The foundation of the Hurricane twin-turbo is a deep-skirt cast-aluminum block with a structural aluminum alloy oil pan. Cross-bolted steel main bearing caps contain the strong rotating assembly of a forged steel crankshaft and forged steel connecting rods.
Building on existing ICE designs
Produced at the Stellantis’ Saltillo Engine Plant in Mexico, the 3.0-liter Hurricane twin-turbo I-6 shares design features, including bore and stroke and cylinder spacing, with the globally produced turbocharged 2.0-liter I-4. In North America, the 2.0-liter engine is currently available in the Jeep Wrangler, Wrangler 4xe, Cherokee and recently launched Grand Cherokee 4xe.
The Hurricane twin-turbo I-6 is the primary internal combustion power plant of the future in North America for vehicles using the STLA Large and STLA Frame platforms.
Stellantis propulsion system engineers employed a suite of state-of-the-art technologies for the Hurricane twin-turbo to deliver reduced emissions and attain big-engine power:
- Two low-inertia, high-flow turbochargers for rapid response to throttle inputs
- Plasma Transfer Wire Arc (PTWA) coating in the cylinder bores for an ultra-thin, low-friction wear surface
- High-pressure (5,075 psi/350 bar) direct fuel injection with pumps (single for SO/dual for HO) actuated by a dedicated chain-driven shaft
- Dual overhead camshafts with wide-range, fully independent variable valve timing
- Fuel-saving engine stop-start (ESS) function with robust starter motor for quick restarts
- Engine-mounted water-to-air charge cooler with a dedicated cooling
- Continuously variable displacement oil pump with integrated scavenge stage
Split turbo feeds
Each turbocharger in the Hurricane twin-turbo I-6 feeds three cylinders. From a performance standpoint, two smaller turbochargers with less inertia spin up faster and deliver boost to the engine at lower rpm than a single, large turbo.
The compressed air passes through an engine-mounted water-to-air charge air cooler to reduce its temperature. Cooler air is denser, enabling better performance via advanced ignition timing, and helping manage in-cylinder temperatures. An electric pump circulates coolant after the engine is shut down to help cool the turbocharger units for enhanced durability.
The high-pressure direct fuel injection system runs at 5,075 psi (350 bar) and uses injectors mounted centrally in the combustion chamber. This design promotes finer atomization and super-fine control of fuel delivery into the cylinder for higher power and lower emissions.
Different turbos for standard and high output
The Hurricane’s turbochargers are optimized for each version. The turbos on the Hurricane SO deliver peak boost of 22 psi, while the Hurricane HO turbos deliver 26 psi of peak boost.
Helping the Hurricane HO deliver its enhanced performance are lightweight, oil-jet cooled, forged aluminum pistons with an anodized top ring land and a diamond-like coating (DLC) on the pins to minimize friction. The Hurricane HO runs with a 9.5:1 compression ratio and uses 91 octane premium fuel.
With a focus on fuel economy, the Hurricane SO uses cast aluminum pistons with cast iron top ring land insert, running with a 10.4:1 compression ratio. It’s use of cooled EGR helps reduce engine pumping losses and manage in-cylinder temperatures. Premium fuel is recommended.
Tough Coating for The Cylinders
Less friction, reduced weight and unparalleled wear resistance from a thermal sprayed microstructure of metallic and oxide components that metallurgically transform are the key benefits of the PTWA coating inside the cylinders, an alternative to the traditional cast-in-place or pressed-in cast iron cylinder liners. The PTWA coating is ultra-thin, compared with 3 to 4 millimeters of a cast iron liner and has 10 times the wear resistance.
The PTWA coating is applied to the Hurricane block during the manufacturing process at the Saltillo North Engine Plant. The process, adapted from the aerospace industry, melts a steel alloy wire at 2,300 degrees Celsius (4,150 degrees Fahrenheit), producing microscopic particles sprayed onto the cylinder walls at high velocities, where the particles splat-cool to form the coating and form a physical bond to the aluminum cylinder bore.
Stellantis
Stellantis N.V. (NYSE / MTA / Euronext Paris: STLA) is one of the world’s leading automakers and a mobility provider. Its storied and iconic brands embody the passion of their visionary founders and today’s customers in their innovative products and services, including Abarth, Alfa Romeo, Chrysler, Citroën, Dodge, DS Automobiles, Fiat, Jeep, Lancia, Maserati, Opel, Peugeot, Ram, Vauxhall, Free2Move and Leasys. Powered by our diversity, we lead the way the world moves – aspiring to become the greatest sustainable mobility tech company, not the biggest, while creating added value for all stakeholders as well as the communities in which it operates. For more information, visit www.stellantis.com.
0 Comments